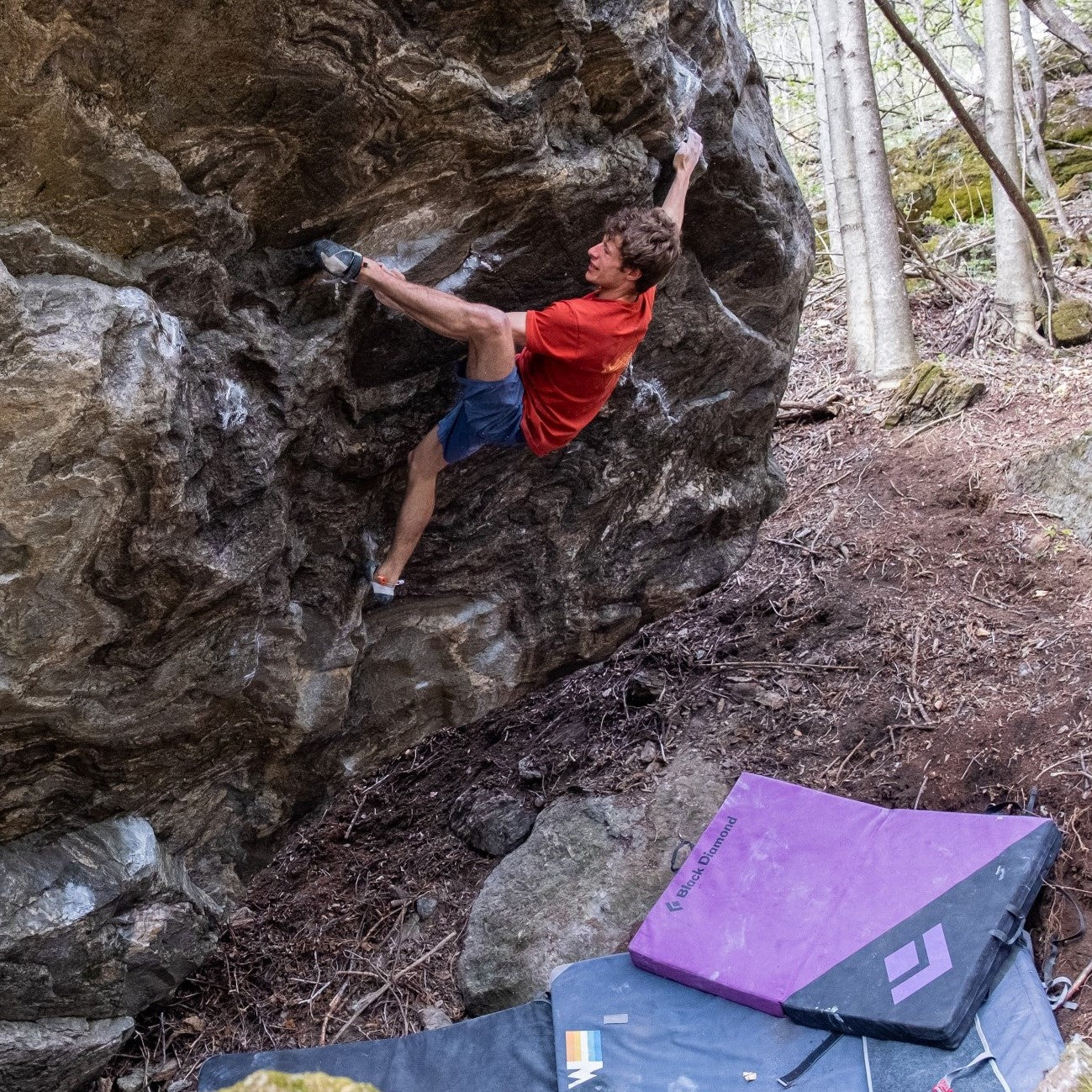
LINES CLIMBING MIXTAPE
BLACK DIAMOND PRESENTS: LINES CLIMBING MIXTAPE
Add 100 EUR more to quality for free Shipping!
€0,00 EUR
WEDNESDAY, DECEMBER 20, 2023
Aluminum is Lighter than Steel
When aluminum ice screws first came onto the scene, the attraction of a lighter weight rack caused many climbers to fully switch over. The weight savings spread across a full rack of 14 screws can be upwards of 800 grams. That is serious weight, especially when it’s hanging off your harness on a steep and technical lead, or on your back for a five-hour approach.
Ultimately this means you could bring more food, more gear, or that huge belay parka, all of which may lead to more success and less suffering. But, other than weight, what are the other performance differences between aluminum and steel ice screws?
Both aluminum and steel ice screws, 13cm or longer, are CE certified and meet the EN 568:2015 10kN (2248 lbf) radial strength requirement. Although the stubby 10cm steel ice screws are not CE certified, they also meet the 10kN radial strength requirement. To put this in perspective, let’s imagine your friend Ken weighs 225lbs when loaded up with all his kit. A well-placed ice screw is rated to hold 10 Kens. It is hard to generate that much force in most real-world climbing scenarios.
Ice screws themselves are very strong, but they rely on the support of the surrounding ice which can be highly variable, especially at the surface. In a textbook placement, with the screw placed at a slightly positive angle (tip higher than the hanger) and the hanger flush to the ice, an applied load will stress the ice surrounding the screw and eventually cause the ice to fail. The surface ice will fracture roughly 3 – 5 centimeters deep surrounding the body of the screw. Once this occurs, the exposed section of the screw body becomes cantilevered and is no longer supported by ice. The now cantilevered screw body, unable to support the load alone, will begin to bend until the hanger is levered off the head, the screw body fails, or the screw pulls out of the ice.
Aluminum is Lighter than Steel
When aluminum ice screws first came onto the scene, the attraction of a lighter weight rack caused many climbers to fully switch over. The weight savings spread across a full rack of 14 screws can be upwards of 800 grams. That is serious weight, especially when it’s hanging off your harness on a steep and technical lead, or on your back for a five-hour approach.
Ultimately this means you could bring more food, more gear, or that huge belay parka, all of which may lead to more success and less suffering. But, other than weight, what are the other performance differences between aluminum and steel ice screws?
Both aluminum and steel ice screws, 13cm or longer, are CE certified and meet the EN 568:2015 10kN (2248 lbf) radial strength requirement. Although the stubby 10cm steel ice screws are not CE certified, they also meet the 10kN radial strength requirement. To put this in perspective, let’s imagine your friend Ken weighs 225lbs when loaded up with all his kit. A well-placed ice screw is rated to hold 10 Kens. It is hard to generate that much force in most real-world climbing scenarios.
Ice screws themselves are very strong, but they rely on the support of the surrounding ice which can be highly variable, especially at the surface. In a textbook placement, with the screw placed at a slightly positive angle (tip higher than the hanger) and the hanger flush to the ice, an applied load will stress the ice surrounding the screw and eventually cause the ice to fail. The surface ice will fracture roughly 3 – 5 centimeters deep surrounding the body of the screw. Once this occurs, the exposed section of the screw body becomes cantilevered and is no longer supported by ice. The now cantilevered screw body, unable to support the load alone, will begin to bend until the hanger is levered off the head, the screw body fails, or the screw pulls out of the ice.
As the ice screw is only as strong as the surrounding ice, placing a screw into less than perfect ice may cause the ice to break down and cone out at much lower loads which leads to an unsupported and cantilevered screw body. This is where the material and geometry make a significant difference.
Without getting too in the weeds, steel has higher ductility and toughness than the heat-treated aluminum used for ice screws. This basically just means that the steel screws can and do bend/deform more than aluminum screws before failure.
Design Priorities
This doesn’t tell the whole story though. Geometry and design priorities play a huge role in this discussion. When Black Diamond designed the steel Express ice screw many moons ago, the priority was to make a robust and durable work horse. Whereas the aluminum BD Ultralight (UL) ice screws were designed to be just that … ultralight. Both ice screw designs meet the 10kN strength requirements of course, but the design priorities are different—right tool for the job sort of thing.
One obvious example of the geometry differences is the the diameter of the screw bodies. As aluminum is a weaker material, the diameter of the UL ice screw is larger to maintain the strength required to pass the CE requirements. The larger diameter can be an advantage when placingrebored screws. It can also make it easier to line up the holes when drilling naked threads and the larger diameter holes make it less likely that the rope will get stuck when pulling your rope.
Evaluating Ice
First, search for that nice homogenous, blue, plastic ice. Then, when placing the screw, pay attention to how much torque is required to turn the screw. You will generally feel consistent resistance during a placement in good ice. If you feel any significant reduction in the torque required to drill the screw, you may have hit a weak layer or an air pocket. If it’s taking a little force to turn the screw and that force is consistent all the way until the hanger meets the carefully cleaned surface ice, then we likely have a very good screw. Good screw placements also generally produce a core during placement.
Ice Quality
If the surface has been hit with sun, heat, or has lost density through sublimation (big word for what happened to your ugly white ice cubes in the freezer after a few months) then it is a lot weaker and will fracture more easily which increases the likelihood of relying on a cantilevered screw body. So, make sure to clean any weak surface ice off before placing your ice screw!
Ice Thickness
Gauge the thickness of the ice. You want to be able to bury the screw to the hanger into good ice without the threads banging into the rock and damaging your screw. And of course, ideally you don’t want the screw protruding from the ice (see screwtusion).
Wet Ice or Very Cold Ice
Aluminum screws tend to bind more on very cold days, or in ice with layers of different temperatures (really wet ice).
At the end of the day, when faced with the situation of placing an ice screw in sub-optimal ice conditions you should search elsewhere to find a better placement. You may have more buffer with a steel ice screw but relying on ice screws in marginal ice is not a good strategy. Taking the time to get good screw placements is very important! The best option, whether you are using steel or aluminum, is to get down to that nice blue plastic ice we all love to see.
Real WorldIt is our responsibility as climbers to choose the best tools for the job and know the limitations of our equipment.
Many people here at BD, including myself and athletes like Will Gadd, use a mixture of aluminum and steel ice screws depending on the objective. This way you can make use of the advantages both models offer. Reboring? Break out the aluminum ice screw with the larger outside diameter. Drilling threads with your 23cm screw? Bring the aluminum screw to make lining up those holes easier and save the weight. Heading out for a glacier walk? Bring those aluminum screws and save some weight. Heading out on a remote backcountry mission where weight is king? Aluminums all the way.
Dealing with a bunch of questionable ice? Break out that steel screw to increase your margins or better yet, ask yourself if climbing the route is worth it. Knowing when to back off rather than risking a fall onto marginal gear is crucial for staying safe in the mountains.
Watch and learn as our Field Test Coordinator runs you through a step by step...
Watch and learn as our Field Test Coordinator runs you through a step by step process of trimming and setting up any STS-style Black Diamond skin.
Every climber has a few lines they dream about. Whether inspired or haunted—or sometimes both—these...
Every climber has a few lines they dream about. Whether inspired or haunted—or sometimes both—these lines can push us beyond what we thought we were capable of, in turn teaching us who we really are. BD Ambassador Ethan Salvo recently restructured his entire life to focus on two climbs that pulled him into the void with only one way out … getting to the top. This is his story of sending Dreamcatcher and becoming the first Canadian to climb V16 in the same week.
BD Athlete Connor Herson spent as many weekends as possible in the Valley this spring...
BD Athlete Connor Herson spent as many weekends as possible in the Valley this spring during a grueling quarter at Stanford. The objective? Ground up, in-a-day ascents.
Follow Hillary in this documentary film capturing her record-breaking ascent of Europe’s tallest peak.
BD Athlete Seb Bouin takes us back to his home crag of Pic Saint-Loup where...
BD Athlete Seb Bouin takes us back to his home crag of Pic Saint-Loup where he establishes the true king line of the cliff—Wolf Kingdom.
A film documenting the often-overshadowed bouldering of Yosemite climbing, where jedis like BD Athlete Carlo...
A film documenting the often-overshadowed bouldering of Yosemite climbing, where jedis like BD Athlete Carlo Traversi have spent years learning to harness the force.
BD Athlete Hazel Findlay shares her tips for returning to the climbing life for new...
BD Athlete Hazel Findlay shares her tips for returning to the climbing life for new mothers.
A film documenting the first flash ascent of El Capitan by BD Athletes Babsi Zangerl...
A film documenting the first flash ascent of El Capitan by BD Athletes Babsi Zangerl and Jacopo Larcher.
BD Athletes Babsi Zangerl and Jacopo Larcher share their story of climbing one of the...
BD Athletes Babsi Zangerl and Jacopo Larcher share their story of climbing one of the world’s most mythical trad routes.
BD Athletes Aaron Mulkey and Yannick Glatthard take the new Hydra into the backcountry of...
BD Athletes Aaron Mulkey and Yannick Glatthard take the new Hydra into the backcountry of Montana in search of steep ice and mixed climbing.
Follow Dorian Densmore and Mya Akins for a month-long, exploratory mission in the Chugach Mountains.
Two BD legends walk into the Valley. What happens next? Watch and see.